Fish Processing
On this page
- What kind of work do people do in a secondary fish processing plant?
- What are some health and safety hazards for fish processors?
- What are the tasks in the Buttered Sole line?
- What are the tasks in the Scallops Line?
- How can we reduce the risk factors for repetitive motion injury (RMI)?
- How can the risk of RMI be reduced on the Buttered Sole Line?
- How can the risk of RMI be reduced on the Scallops Line?
What kind of work do people do in a secondary fish processing plant?
Back to topIn a secondary fish processing plant, workers are involved in such tasks as the buttering, breading, stuffing and packaging of fish that has already been de-boned and filleted in a primary processing plant. All the operations are organized on a conveyor line.
The buttered sole line and the scallops line were selected as the most representative operations in a secondary fish processing plant.
What are some health and safety hazards for fish processors?
Back to top- Possible noise exposure.
- Slips, trips, and falls.
- Stress.
- Shift work or extended work days.
- Working in a standing position.
In addition to some of the hazards listed above, pain or injury from physical overexertion, repetitive manual tasks, or working in awkward positions is very common. A case study is presented below.
Please also see the OSH Answers on Conveyors – ergonomics for more information.
What are the tasks in the Buttered Sole line?
Back to topTasks on the buttered sole line consist of spreading, buttering, breading, packaging, and wrapping filet of sole. Such tasks as buttering and breading are automated. Therefore, we will look only at the spreading, packaging and wrapping tasks.
What is Spreading?
The spreading task consists of scattering the frozen sole on the conveyor (Figure 1). Workers stand to perform this task for the entire shift. The conveyor is 82-104 cm high and 50 cm wide. To spread the fish on the conveyor, workers have to reach forward with their arms above waist level. They use the same movements over and over.
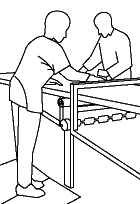
Figure 1 - Spreading
What are the risk factors of Spreading?
Prolonged standing in a stooped position, repetitious reaching forward and twisting of the body put workers at high risk for low back injury.
Working with arms elevated above the waist level, and having no control over the pace of work pose a considerable risk for injuries of the neck, shoulder and arms.
Standing on a hard floor and having limited flexibility of body posture can cause lower leg discomfort.
What is Packaging?
Packaging consists of filling boxes with one kilogram of buttered and breaded filet of sole (Figures 2 and 3). To complete the task, a worker has to:
- pick up and unfold a carton to make a box
- place the box on a scale and line the box with plastic wrap
- pick up fish from the container and put it into the box
- place the box on the conveyor
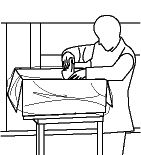
Figure 2 - Packaging
One work cycle lasts two seconds and can be classified as highly repetitive. Packaging is done while standing.
What are the risk factors of Packaging?
The packaging job poses the risk for repetitive motion injuries because of improper layout of the work station, the fast pace of work and the design of the task that does not allow workers to change activities throughout the work shift.
Restricted flexibility of body positions, highly repetitive movements of both arms above the waist level and repetitious reaching sideways and forward put workers at high risk for injuries of the neck, shoulders and upper arms.
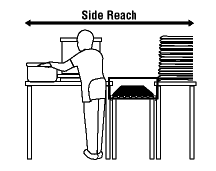
Figure 3 - Packaging
Prolonged standing, restricted flexibility of body position and repetitious twisting pose a risk for low back pain and lower leg discomfort.
What is Wrapping?
The wrapping of boxes is carried out by two workers using two sealing machines. Each worker processes about 3,000 boxes every shift (Figure 4). To complete the task, a worker has to:
- twist the body to the left to reach for the box on the conveyor
- twist the body to the right to insert box into cellophane bag
- press control button to activate sealer
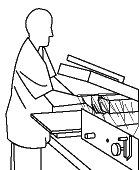
Figure 4 - Wrapping
The task lasts approximately five seconds and is carried out while standing.
What are the risk factors of Wrapping?
The wrapping job poses a risk for repetitive motion injuries because of the poor layout of the work station, the fast pace of work dictated by the speed of the conveyor, and the design of the task, that does not allow workers to change activities throughout the whole shift.
Workers are at risk for neck, shoulder and upper arm injuries because of restricted flexibility of body positions, highly repetitious movements of both arms above waist level and repetitive reaching sideways.
Highly repetitive and forceful movements while handling one kilogram boxes with only one hand are potentially hazardous to the wrists.
Prolonged standing and frequent twisting create hazards for low back and lower leg injuries.
What are the tasks in the Scallops Line?
Back to topThe scallops line consists of a variety of tasks with different levels of automation. Stuffing and rolling, wrapping and packaging are the most representative tasks for the scallops line.
What is Stuffing?
Stuffing consists of placing certain types of ingredients on a fillet (Figure 5) and then rolling the fillet into a ball shape (Figure 6). To complete the task, a worker has to:
- pick up a fillet and place it on the scale
- pick up a handful of stuffing and place it on the fillet
- roll the fillet
- place the stuffed fillet on the conveyor
The task lasts approximately four seconds. Workers stand to perform this task for the entire shift.
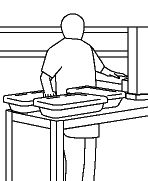
Figure 5 - Stuffing
What are the risk factors of Stuffing?
The stuffing job poses a risk for repetitive motion injuries because of the improper layout of the work station, limited control over the pace of work and a task design that does not allow workers to change activities throughout the work shift.
Highly repetitive hand manipulation while stuffing puts workers at risk for injuries of the wrists.
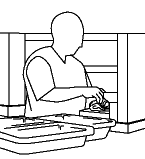
Figure 6 - Stuffing
Highly repetitive movements of the upper limbs and sustained muscular tension in the neck and shoulder region create hazards for the neck, shoulders and arms.
Prolonged standing and frequent twisting of the body create hazards for low back and lower leg injuries.
What is Wrapping?
Wrapping consists of putting the frozen fillet into a cellophane bag (Figure 7). The bag is opened by blowing air at it. To complete the task, a worker has to
- reach for a fillet from a revolving carousel
- put the fillet into the bag
- place the bag on a conveyor
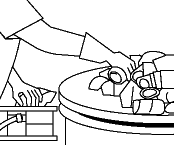
Figure 7 - Wrapping
The task lasts approximately 1.5 seconds. Workers may perform this task for the entire shift.
What are the risk factors of Wrapping?
The extremely unsuitable layout of the workstation and the highly repetitive and fast movements required while wrapping make this task very hazardous for repetitive motion injuries.
The neck and shoulder and every muscle and joint of the upper limbs are at risk.
The low back is also at risk due to awkward body positions, asymmetric loading and frequent twisting. Prolonged standing in a stooped position due to the lack of foot clearance adds a risk for injury to the lower legs.
What is Packaging?
The packaging task consists of putting the individually wrapped fillet into boxes (Figure 8). To complete the task, a worker has to:
- reach for the fillet using both hands
- pick up the fillet from a revolving carousel
- place the fillets into boxes
The task lasts approximately one second. Workers may perform this task for the entire shift.
What are the risk factors of Packaging?
Improper layout of the workstation, a fast pace of work and the task design create hazards for repetitive motion injuries.
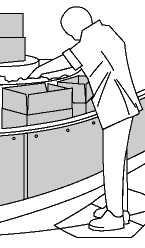
Figure 8 - Packaging
The neck and shoulders, due to the sustained muscular load, are at the highest risk. Due to repetitive manipulation, the wrists are also at considerable risk for injuries.
Prolonged standing in a stooped position due to the lack of leg clearance makes packaging hazardous for low back and lower leg injuries.
How can we reduce the risk factors for repetitive motion injury (RMI)?
Back to topPoor workstation layouts, the conveyor-driven pace of work and the lack of variety of tasks through the work shift are the conditions that pose risks to develop repetitive motion injuries in a secondary fish processing plant. The Ergonomics section of OSH Answers has more information on RMI risk factors.
One of the main risk factors is the repetitiveness of the work.
To change the repetitive pattern of the work a worker needs to do different tasks. The assembly-line type of work in the secondary fish processing plant makes it difficult to build a variety of activities in the workers' duties. However, there are a few options to consider.
Job rotation - Rotating jobs within one work shift can reduce the damaging effects of repetitive work. There are some benefits even where rotation occurs between similar tasks. The feeling of change reduces monotony and slows down the development of fatigue.
Teamwork - The other possible approach is to use teamwork. Assigning the operation of the whole assembly line to a group of workers and giving them control of all aspects of the work improves attitude and work satisfaction which are important in preventing injuries.
The recommendation for job rotation or team work applies to both the buttered sole and the scallops lines in the fish processing plant. If the re-designing of tasks is not possible, the implementation of 5 - 10 minute breaks every hour can lessen the impact of repetitive work.
Awkward postures and movements due to unsuitable workstation designs are the second major area of concern.
How can the risk of RMI be reduced on the Buttered Sole Line?
Back to topThe buttered sole operation consists of:
- spreading
- packaging
- wrapping
Spreading
Workers involved in the spreading of fish are mainly exposed to repetitive movements and awkward body positions.
To reduce awkward postures, provide shorter workers with platforms so that they can spread the fish with their arms below waist level. There should be enough foot clearance to allow workers to get as close as possible to the conveyor. Having a foot rest would allow workers to shift their body weight (Figure 9).
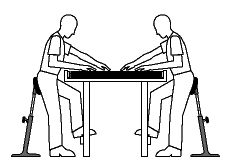
Figure 9 - Spreading
A sit/stand stool would reduce the stress on the legs and back due to prolonged standing. Also, wearing gloves when handling frozen fish would reduce the chance of losing manual dexterity from the cold.
Packaging
Workers involved in the packaging of the fish are exposed to repetitive movements and awkward body positions.
To reduce awkward postures, it is necessary to rearrange the work materials (Figure 10). Tilting the container of fish would reduce bending the wrists and elevating the elbows. Placing the cartons in front of the worker would eliminate reaching sideways.
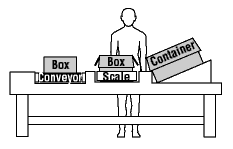
Figure 10 - Packaging
Shorter workers should use platforms so that they can pick up the fish with their arms at waist level. The work bench should have foot rests so that workers can shift their body weight. Anti-fatigue matting and a sit/stand stool would help to reduce the stress on the legs and back from prolonged standing.
Wrapping
Workers involved in the wrapping of boxes are exposed to repetitive and forceful movements and awkward body positions.
To avoid using awkward postures, workers should pick up boxes with their arms at waist level. Shorter workers should use a platform. To reduce reaching sideways, it may be necessary to modify the flow of the conveyor (Figure 11).
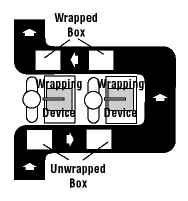
Figure 11 - Wrapping
Workers should have enough foot clearance so that they can get close to the work bench. They should also have a foot rest to shift their body weight. Providing workers with anti-fatigue matting and a sit/stand stool would release stress on their legs and back due to prolonged standing.
How can the risk of RMI be reduced on the Scallops Line?
Back to topThe scallops operation consists of:
- stuffing
- wrapping
- packaging
Stuffing
Workers involved in the stuffing of fillets are exposed to repetitive movements and awkward postures.
To reduce awkward postures it is necessary to use platforms so that workers can use their arms at waist level. Reaching sideways can be reduced by rearranging the work materials.
To avoid bending of the wrist, it is necessary to have the scale and the two containers at the same level as the work surface (Figure 12).
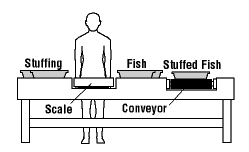
Figure 12 - Stuffing
Workers should have a foot rail to shift their body weight. Using a sit/stand stool and anti-fatigue matting would reduce the stress on the body due to prolonged standing.
Wrapping
Workers involved in the wrapping of the fillets are exposed to repetitive movements and awkward body positions.
To eliminate the repetitive nature of the task requires a major engineering change - the aim would be to fully automate the task. However, the repetitive pattern of work can be changed by rotating workers to other tasks. It would also be beneficial to put into effect a break for every hour of work. This break should be used to relax the muscles.
To reduce awkward body positions such as reaching, workers should have enough leg clearance so that they can get close to the work surface. The wrapping/sealing surface should be at the same height as the carousel (Figure 13). Provide shorter workers with platforms so that they can reach the scallops with their arms at waist level. A sit/stand stool would reduce the stress on the legs and back due to standing for a long time.
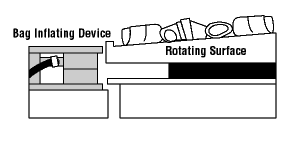
Figure 13 - Wrapping
Packaging
Workers involved in the packaging of fillets are exposed to repetitive movements and awkward body positions.
The repetitive pattern of work can be changed by rotating workers to other tasks. It would also be beneficial to put into effect a break every hour of work. This break should be used to relax the muscles.
To reduce awkward body positions, workers should have enough leg clearance so that they can get close to the work surface (Figure 14). Workers should also have a foot rail to shift the weight of the body from one foot to the other. Platforms should be provided to shorter workers so that they can reach the scallops with their arms at, or below, waist level. A sit/stand stool would reduce the stress on the legs and back due to prolonged standing.
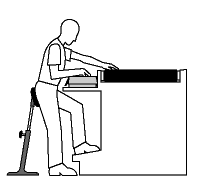
Figure 14 - Packing
Acknowledgement
The Canadian Centre for Occupational Health and Safety in co-operation with the Government of Newfoundland and Labrador, Department of Employment and Labour Relations, Occupational Health and Safety Branch would like to acknowledge the participation of Burin Secondary Processing (A Division of Fishery Products International) who so freely gave their time and resources to assist us in the development of this case study.
- Fact sheet confirmed current: 2022-02-28
- Fact sheet last revised: 2022-02-28