Lockout/Tag out
On this page
- What is Lockout/Tag out?
- What does de-energization mean?
- Why is lockout/tag out important?
- What is the purpose of a lockout/tag out program?
- Who is responsible for the lockout program?
- What details should the lockout procedures and work instructions contain?
- What are the basic steps of locking and tagging out a system?
What is Lockout/Tag out?
Back to topLockout is defined in the Canadian standard CSA Z460-20 "Control of Hazardous Energy - Lockout and Other Methods" as the "placement of a lockout device on an energy-isolating device in accordance with an established procedure." A lockout device is "a mechanical means of locking that uses an individually keyed lock to secure an energy-isolating device in a position that prevents energization of a machine, equipment, or a process."
Lockout is one way to control hazardous energy. See the OSH Answers Hazardous Energy Control Programs for a description of the types of hazardous energy and required elements of a control program.
In practice, lockout is the isolation of energy from the system (a machine, equipment, or process) that physically locks the system in a safe mode. The energy-isolating device can be a manually operated disconnect switch, a circuit breaker, a line valve, or a block (Note: push buttons, selection switches and other circuit control switches are not considered energy-isolating devices). In most cases, these devices will have loops or tabs which can be locked to a stationary item in a safe position (de-energized position). The locking device (or lockout device) can be any device that has the ability to secure the energy-isolating device in a safe position. See the example of the lock and hasp combination in Figure 1 below.
Tag out is a labelling process that is always used when lockout is required. The process of tagging out a system involves attaching or using an information tag or indicator (usually a standardized label) that includes the following information:
- Why the lockout/tag out is required (repair, maintenance, etc.).
- Time and date of application of the lock/tag.
- The name of the authorized person who attached the tag and lock to the system.
Note: ONLY the authorized individual who placed the lock and tag onto the system is the one who is permitted to remove them. This procedure helps make sure the system cannot be started up without the authorized individual's knowledge.
What does de-energization mean?
Back to topDe-energization is a process that is used to disconnect and isolate a system from a source of energy to prevent the release of that energy. By de-energizing the system, the risk that the system could inadvertently, accidentally, or unintentionally cause harm to a person through the release of hazardous energy is eliminated.
Why is lockout/tag out important?
Back to topSafety devices such as barrier guards or guarding devices are installed on systems to maintain worker safety while these systems are being operated. When activities such as maintenance, repair, or set-up or the removal of jams, clogs or misaligned feeds are performed, these safety devices may be removed if other controls are in place to reduce or eliminate the hazards.
A lockout/tag out program and procedures for these scenarios will reduce the risk of injury due to the unintended or inadvertent release of hazardous energy.
What is the purpose of a lockout/tag out program?
Back to topThe purpose of a lockout/tag out program is to control hazardous energy. A lockout program should:
- Identify the types of:
- Hazardous energy in the workplace
- Energy-isolating devices
- De-energizing devices
- Guide the selection and maintenance of protective devices, hardware, and personal protective equipment (PPE)
- Assign duties and responsibilities
- Describe lockout procedures for all machines, equipment, and processes
- Determine shutdown, de-energizing, energizing, and start-up sequences
- Describe training requirements for authorized and affected workers
- Be audited for effectiveness
An effective lockout/tag out program will help prevent:
- Contact with a hazard while performing tasks that require the removal, by-passing, or deactivation of safeguarding devices.
- The unintended release of hazardous energy (including stored energy).
- The unintended start-up or motion of machinery, equipment, or processes.
Who is responsible for the lockout program?
Back to topEach party in the workplace has a responsibility in the lockout program. In general:
Management is responsible for:
- Drafting, reviewing, and updating the lockout program and procedures.
- Identifying the employees, machines, equipment, and processes included in the program.
- Providing the necessary protective equipment, hardware and appliances.
- Monitoring and measuring conformance with the program.
Supervisors are responsible for:
- Distributing protective equipment, hardware, and any appliance and ensuring its proper use by employees.
- Making sure that equipment-specific procedures are established for the machines, equipment and processes in their area.
- Making sure that only properly trained employees perform service or maintenance that require lockout.
- Making sure that employees under their supervision follow the established lockout procedures where required.
Authorized individuals are responsible for:
- Following the procedures that have been developed.
- Reporting any problems associated with those procedures, the equipment, or the process of locking and tagging out.
Note: The Canadian standard CSA Z460-20, Control of Hazardous Energy - Lockout and Other Methods contains more information and many informative annexes about various risk assessments, lockout situations, and other control methods.
What details should the lockout procedures and work instructions contain?
Back to topAn organization will have one overall lockout program; however, for each unique machine or equipment, there will be a detailed procedure or work instruction that describes the steps to control the hazardous energy.
The written lockout procedure should specify:
- The specific machine, equipment, or process involved in the shutdown and isolation process.
- The hazardous energy present and the type of energy-isolating or de-energizing devices required.
- Where the lockout devices are required and how they are installed.
- The steps for shutting down, isolating, blocking, securing, and relieving stored or residual energy.
- The steps for placing and removing all lockout devices.
- How the isolation can be verified.
- How others in the area will be informed of the lockout and the return to service.
Procedures and work instructions identify how the lockout process will be carried out and may include pictures or images of what is being described.
What are the basic steps of locking and tagging out a system?
Back to topLockout and tag out processes involve more than putting a lock on a switch. They are comprehensive step-by-step processes that involve communication, coordination, and training.
Please note the following definitions from CSA Z460-20:
Affected person - persons who are not directly involved in the work requiring the hazardous energy control, but who are (or may be) located in the work area.
Authorized person - a person who is qualified to engage in hazardous energy control because of knowledge, training, and experience and has been assigned to engage in such control.
General steps of a lockout/tag out procedure include:
1. Prepare for Shutdown
The authorized person will identify the machine, equipment, or process that requires lockout, which sources of energy are present and must be controlled, and what lockout device will be used. This step involves gathering all required equipment (e.g., lockout devices, tags, etc.).
2. Notify all Affected Personnel
The authorized person will communicate the following information to notify affected persons:
- What is going to be locked/tagged out.
- Why it is going to be locked/tagged out.
- For approximately how long the system be unavailable.
- Who is responsible for the lockout/tag out, if not themselves.
- Who to contact for more information.
This information should also be present on the tag required for the lockout.
3. Equipment Shutdown
Follow shutdown procedures (either established by the manufacturer or employer). Equipment shutdown involves ensuring controls are in the off position and verifying that all moving parts, such as flywheels, gears, and spindles, have come to a complete stop.
4. Isolation of System (De-energization)
Follow the lockout procedure for the identified machine, equipment, or process. Review the following isolation practices for various forms of hazardous energy:
- Electrical energy - Switch electrical disconnects to the off position. Visually verify that the breaker connections are in the off position. Lock the disconnects into the off position. NOTE: Only disconnect switches or breakers that you are trained or authorized to do so, especially at high voltages.
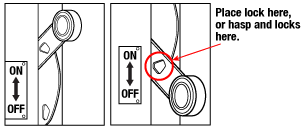
Figure 1: Electrical lockout
- Hydraulic and pneumatic potential energy – Set the valves in the closed position and lock them into place. Bleed off the energy by slowly opening the pressure relief valves. Some procedures for pneumatic energy control may require that pressure relief valves be locked in the open position. Some procedures for hydraulic energy, for example, in lifting devices, may require blocking.
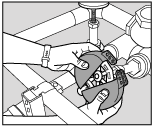
Figure 2: Hydraulic and pneumatic lockout
- Mechanical potential energy - Carefully release energy from springs that may still be compressed. If this is not feasible, block the parts that may move if there is a possibility that the spring can transfer energy to it.
- Gravitational potential energy - Use a safety block or pin to prevent the part of the system that may fall or move.
- Chemical energy - Locate chemical supply lines in the system and close and lockout the valves. Where possible, bleed lines and/or cap ends to remove chemicals from the system.
For more types of energy, see Hazardous Energy Control Programs.
5. Dissipation (Removal) of Residual or Stored Energy
In general, examples include:
- Electrical energy – To find a specific method to discharge a capacitor for the system, contact the manufacturer for guidance. Many systems with electrical components, motors, or switch gears contain capacitors. Capacitors store electrical energy. In some cases, capacitors hold a charge and may release energy very rapidly. In other cases, capacitors are used to remove spikes and surges to protect other electrical components. Capacitors must be discharged in the lockout process to protect workers from electrical shock.
- Hydraulic and pneumatic potential energy – Setting the valves in the closed position and locking them into place only isolates the lines from more energy entering the system. In most cases, residual energy will still be left in the lines as pressurized air or fluid. This residual energy can be removed by bleeding the lines through pressure relief valves. Verify depressurization or use flange-breaking techniques. Contact the manufacturer for more specific details, or if no pressure relief valves are available, what other methods are available.
- Gravitational potential energy – If possible, bring the equipment or machine to ground level.
- Chemical energy – If available, bleed lines and/or cap ends to remove chemicals from the system.
6. Lockout/Tag Out
When the system's energy sources are locked out, specific guidelines must be followed to make sure that the lock cannot be removed and the system cannot be inadvertently operated. These guidelines include:
- Each lock should only have one key (no master keys are allowed).
- All keys must be removed from locks and kept with the person who applied the lock.
- There should be as many locks on the system as there are people working on it. For example, if a maintenance job requires 3 workers, then 3 locks should be present – each individual must place their OWN lock on the system. Locks can only be removed by those who installed them and should only be removed using a specific process – see step 9 below.
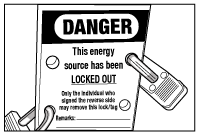
Figure 3: Example of multiple locks on a lockout tag
7. Verify Isolation
Verify that the system is properly locked out before beginning any work. Verification can take place in several ways:
- The machine, equipment, or process controls (push buttons, switches, etc.) are engaged or activated, and the result is observed. No response means isolation is verified. Return controls to the safe position (off).
- Visual inspection of:
- Electrical connections to make sure they are open.
- Suspended parts are lowered to a resting position or blocked to prevent movement.
- Other devices that restrain machine or process movement.
- Valve positioning for double block and bleed (for pipes or ducts) - closing two valves of a section of a line and then bleeding (or venting) the section of the line between the two closed valves.
- Presence of solid plate used to absolutely close a line - called line blanking (for pipes or ducts).
- Any other acceptable method of energy isolation.
- Testing of the equipment:
- Test circuitry (should be done by a certified electrician) - Note: equipment with capacitors must be cycled until all energy is drained.
- Check pressure gauges to make sure hydraulic and pneumatic potential energy has been removed.
- Check temperature gauges to make sure thermal energy has been discharged.
Choose the method that will make sure that the energy to the system has been isolated without creating other hazards during the verification.
8. Perform Maintenance or Service Activity
Complete the activity that required the system to be locked out.
9. Remove Lockout/Tag out devices
To remove locks and tags from a system that is now ready to be put back into service, the following general procedure can be used:
- Inspect the work area to make sure all tools and items have been removed.
- Confirm that all employees and persons are safely located away from hazardous areas.
- Verify that controls are in a neutral position.
- Remove devices in the opposite order in which they were installed and re-energize the system.
- Notify affected employees that servicing is completed.
*Note: It is good practice to make sure the individuals who placed a lock on the system are present when the system is restarted. This practice helps make sure those employees working on the system are not in a hazardous area when the machine is restarted.
- Fact sheet last revised: 2021-11-23