Hotel Laundry- Case Study
On this page
- What kind of work do people do in the hotel laundry?
- What are the tasks involved in "sorting and washing"?
- What are the ergonomic risk factors of "sorting and washing"?
- What are the tasks involved in "drying/ironing and folding"?
- What are the risk factors when feeding the rolling ironer?
- What are the tasks involved in retrieving and folding pieces of laundry?
- What are the risk factors of retrieving pieces of laundry from the rolling ironer?
- What are the tasks involved in folding towels?
- What are the risk factors involved in folding towels?
- How can we reduce the risk factors for RMI?
What kind of work do people do in the hotel laundry?
Back to topIn this case study, a team of eight workers are responsible for the laundry of linen and towels in a hotel. The laundry process is divided in two operations:
- sorting and washing all laundry and drying towels only, and
- drying and folding bedsheets, pillowcases
Two workers sort and wash all laundry; and dry and fold the towels. Six workers dry and fold the bedsheets and pillowcases.
What are the tasks involved in "sorting and washing"?
Back to topThis case study considers a simplified laundering process. It is assumed that the hotel has high-performance commercial washers that remove a significant amount of water from the linens. When this system is used, linens can be fed directly through a rolling ironer that has an integrated folding system for large pieces of laundry. Towels are dried in a drum-type drier.
Housekeepers use a laundry chute to get the dirty linen from the upstairs down to the laundry area. The "sorting and washing" operation involves the following:
- sorting laundry
- loading bins which weigh 27 kg (60 lbs) with dry laundry, and 55 kg (120 lbs) when laundry is wet
- transporting (pushing/pulling) bins to washer
- weighing the laundry according to the capacity of the washing machine
- loading washer
- unloading washer
- transporting (pushing/pulling) bins to dryer (towels only)
- loading dryer with towels
- unloading towels from the dryer
In one eight-hour shift, 20 bins of laundry are processed by two workers (Figure 1). The dry laundry is handled four times – 27 kg (60 lbs) x 4 handlings x 20 bins = 2,200 kg (4,800 lbs); the wet laundry is handled twice – 55 kg (120 lbs) x 2 handlings x 20 bins = 2,200 kg (4,800 lbs). The workload is distributed evenly, so each worker handles approximately 2,200 kg (4,800 lbs) of laundry every day.
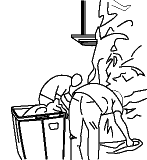
Figure 1 - Sorting laundry
The handling of the laundry requires the use of considerable force:
- pulling soiled laundry from the pile under the chute and loading the laundry bins (Figure 2, 3)
- loading laundry into the washer (Figure 4)
- pulling wet laundry from the washer (Figure 5)
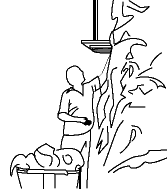
Figure 2 - Sorting laundry
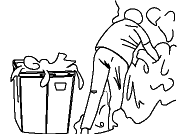
Figure 3 - Sorting laundry
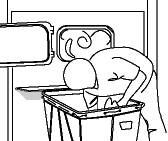
Figure 4 - Loading the washer
These movements are particularly stressful on the hands, wrists and shoulders.
Handling the laundry requires whole body motions beyond acceptable ranges. Reaching above the shoulder, bending to the floor (Figure 5) and twisting are examples. Also, the job is carried out while standing on a concrete floor which adds stress to the feet and legs as well as to the rest of the body. In addition to the ergonomic risk factors, the persons handling and washing soiled laundry may be exposed to the following risks:
- contracting an infectious disease
- exposure to chemical substances such as detergents and bleaches.
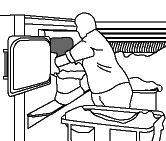
Figure 5 - Pulling wet laundry from the washer
What are the ergonomic risk factors of "sorting and washing"?
Back to topThe Ergonomics section of OSH Answers has more information on RMI risk factors. Carrying out the "sorting and washing" tasks can be hazardous to the workers. There are three major risk factors:
- The heavy work load (handling over 2 tonnes of laundry per shift) combined with bodily motions beyond safe ranges create risk for back injuries.
- Frequent and forceful movements (while pulling/pushing the laundry) and forceful grips create a high risk for wrist and other upper limb injuries.
- Working while standing/walking on a hard floor creates the risk for lower leg discomfort and accelerates the development of fatigue.
These factors have a compounding effect. In other words, each of them increases the effect of the others.
What are the tasks involved in "drying/ironing and folding"?
Back to topIn this operation there are three workstations at which five different tasks are performed:
- reaching for the wet laundry from the laundry basket (Figure 6)
- feeding the rolling dryer with small pieces of laundry (Figure 7)
- spreading large pieces of laundry and feeding them through the rolling ironer (Figure8 and 9)
- retrieving and folding small pieces of laundry from the rolling dryer (Figure 10 and 11)
- retrieving large pieces of laundry from the rolling dryer (Figure 11 and 12)
- folding towels (Figure 13)
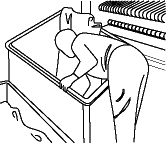
Figure 6- Reaching for the laundry
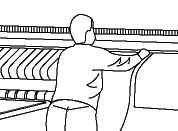
Figure 7 - Feeding small pieces through the rolling dryer
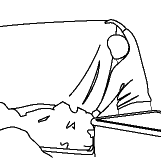
Figure 8 - Spreading large pieces of laundry
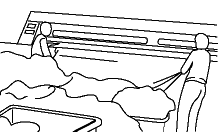
Figure 9 - Feeding the heated-roll ironers with large pieces of laundry
Figures 10 - Retrieving small pieces of laundry from the rolling ironer
Figures 11 – Retrieving large pieces of laundry from the rolling ironer
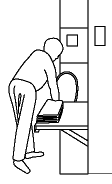
Figure 12 – Retrieving large pieces of laundry
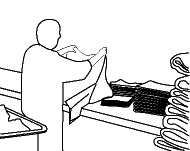
Figure 13 Folding Towels
Small pieces of laundry such as pillowcases are fed through the roller ironer by one worker. To perform this task the worker:
- reaches for the laundry in the bin (Figure6)
- unfolds and stretches the laundry
- spreads the laundry on rollers (Figure 7)
To feed the ironer with laundry such as bed sheets, two workers form a team (Figure 8). This task involves the following:
- reaching for bedsheets in the bin (Figure6)
- unfolding the bedsheets
- spreading the bedsheets (Figure 8)
- spreading the bedsheets on rollers (Figure 9)
What are the risk factors when feeding the rolling ironer?
Back to topSeveral aspects of feeding the ironer with both small and large pieces of laundry pose the risks for repetitive motion injuries. Workers are at a high risk for upper arm, neck, and shoulder injuries because of:
- limited control over the pace of work,
- highly repetitious movements (one task lasts approximately 3 to 8 seconds),
- working with arms at or above shoulder level, and hand manipulation while handling the laundry.
Bending and twisting, reaching forward and upward, and standing in a leaning-forward position contribute to low back pain. Prolonged standing on a hard floor contributes to lower leg discomfort and speeds up the development of muscular fatigue. All of these factors have a compounding effect. In other words, each of them increases the effect of the others.
What are the tasks involved in retrieving and folding pieces of laundry?
Back to topTo retrieve small laundry such as pillowcases from the ironer a worker performs the following movements:
- reaches forward to pick up the laundry
- sets them on a folding table (Figure 10 and 11)
- folds the laundry
To retrieve big pieces of laundry such as bedsheets, which come out of the dryer partially folded (Figure 12), a worker performs the following movements:
- bends and reaches for the bedsheet
- folds the bedsheet
- piles the bedsheet
What are the risk factors of retrieving pieces of laundry from the rolling ironer?
Back to topWorkers involved in retrieving small pieces of laundry are at risk for repetitive motion injuries. The hazardous conditions are:
- no control over pace of work
- repetitive movements
- constrained work posture
- leaning forward standing position
- reaching forward beyond recommended range
- working with extended arms
- standing on a hard floor
The lack of control over the pace of work, highly repetitious movements, constrained work posture, and extended arms while working create a high risk for RMIs. Neck, shoulders and upper arms are at the highest risk for injuries. Leaning forward, over-reaching and prolonged standing in a restricted position put workers at high risk for low back injury. Prolonged standing on a hard floor contributes to lower leg discomfort and speeds up the development of muscular fatigue.
Workers involved in retrieving big pieces of laundry are at risk for repetitive motion injuries, including low back pain. The hazardous conditions are:
- prolonged stooped standing position due to a low work surface
- repetitive movements
- standing on a hard floor
- no control over the pace of work
Contributing factors are prolonged, restricted, and stooped working positions and bending. There is also a risk for injuries of the neck and shoulders. Prolonged standing on a hard floor contributes to lower leg discomfort and speeds up the development of muscular fatigue. All of these factors have a compounding effect. In other words, each of them increases the effect of the others.
What are the tasks involved in folding towels?
Back to topTowels are dried in a drum type dryer. Dry towels are placed in a bin and are sorted according to size and then folded (Figure 13). This task involves the following:
- reaching into the bin
- grasping the towels
- folding the towels
- piling the towels according to size
What are the risk factors involved in folding towels?
Back to topWorkers performing this task are at risk for repetitive motion injuries, including low back pain. The hazardous conditions are:
- continuously bending and twisting
- working with extended arms
- standing on a hard floor
Folding towels puts workers at risk for neck and shoulder injuries. Bending and twisting pose the risk for back injuries. Prolonged standing on a hard floor contributes to lower leg discomfort and low back pain.
How can we reduce the risk factors for RMI?
Back to topGeneral
Continual twisting and reaching while working with extended arms can contribute to the development of repetitive motion injuries. However, the risk for such injuries while folding towels is somewhat lower than for the " ironing and folding" of bedsheets and pillowcases. Some control over the pace of work and some flexibility in the working postures are responsible for the reduced risk.
Let's see how we can improve the operations in this hotel laundry facility:
Sorting and Washing
In the laundry processing, the "sorting and washing" operations are typically manual material handling tasks. These tasks pose the risk for low back pain.
Manual material handling cannot be fully eliminated but it is possible to reduce it by reorganizing the flow of work. For example, instead of sorting towels and linen before loading them into the bins, it would be preferable to load the laundry in the bins directly from the pile under the chute. This would eliminate handling the same laundry twice.
Further improvements of working conditions can be achieved by reducing stressful body movements while handling the laundry. Shortening the laundry chute (pipe) through which laundry is dropped would create more space so that the laundry would not compress against the pipe itself. As a consequence, the sorting of the laundry would require less pulling force.
To reduce bending while reaching for the laundry at the bottom of the bins, it would be advisable to use different types of bins. For example, a bin with one side that opens mounted on a moveable tilt/lift table (Figure 14).
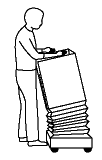
Figure 14 - Tilt-lift table
To reduce pulling and pushing while maneuvering the bins full of laundry, it would be advisable to use lighter bins with wheels designed for hard floors. In addition, the bins should be maintained regularly with particular attention to the wheels.
Working in the "sorting and washing" areas requires prolonged standing on a concrete floor which may lead for lower leg discomfort and fatigue. Ways prevent lower leg discomfort and fatigue are:
- wearing comfortable shoes that provide good cushioning,
- using proper inserts to lessen the stress on the feet and on the lower back, and
- using anti-fatigue matting if practica
- Diseases, Disorders and Injuries (various)
- COVID-19 Tips for Hotels, Motels and Other Accommodations
- How to Work Safely with - Hazardous Products using the "Exclamation Mark" Pictogram
- Working with Household (Chlorine) Bleach
Drying/Ironing and Folding
The overall workload, poor layout of the workstation, improper design of the laundry bins and the repetitiveness of the work are the major risk factors for repetitive motion injuries in the "drying/ironing and folding" job.
Providing bins with one side that opens on elevating devices would reduce bending and other awkward body positions while reaching for towels at the bottom of the bins.
To reduce awkward body positions such as reaching above shoulder level while feeding the dryer/ironer, it would be advisable to use a platform. Narrowing any counter that separates the worker from the dryer would reduce reaching forward.
Retrieving pieces of laundry from the roller ironer and folding towels
To reduce awkward body positions such as reaching above shoulder level while retrieving pillowcases from the ironer it would be advisable to use a platform (Figure15). Narrowing the counter that separates the worker from the ironer would reduce reaching forward. Workers should have a sit/stand stool available to rest between tasks. Also, a foot bar to allow the worker to switch the weight of the body from one foot to the other should be made available.
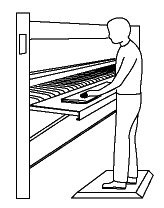
Figure 15 - Standing on a platform while retrieving laundry
Partially folded bedsheets coming out of the rolling ironer should be collected in a basket (Figure 16) so that when completing the folding operation, a worker can use a counter of appropriate height to reduce excessive bending.
To reduce discomfort due to prolonged standing while folding towels, anti-fatigue matting should be used. Also, a sit-stand saddle chair and a foot bar should be provided (Figure 17).
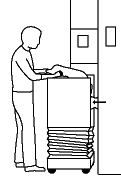
Figure 16 - Collecting bedsheet in a basket
If it is not practical to sit while performing the task, workers should use these devices between tasks.
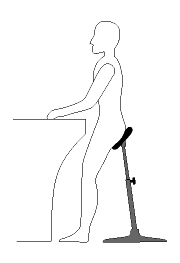
Figure 17 - A sit-stand saddle chair
General Recommendations
One of the main risk factors for repetitive motion injuries in the laundry is the repetitiveness of the work. Incorporate different tasks to change the repetitive patterns of work. Job rotation and team work are two options that allow workers to vary tasks.
Job rotation requires workers to move between different tasks at fixed or irregular periods of time. Workers in the laundry cannot fully benefit from job rotation because all the tasks are similar in nature. Still, the feeling of change reduces monotony and slows down the development of fatigue.
In team work, workers form a team and each member of the team shares several different tasks. The whole team is involved in the planning of the work. The team controls all aspects of work. This improves attitude and job satisfaction, which are important factors in the prevention of occupational injuries and diseases.
This study focuses on ergonomic risks.
For more information about the other hazards to which laundry workers may be exposed, see documents:
Acknowledgement
The Canadian Centre for Occupational Health and Safety in co-operation with the Government of Newfoundland and Labrador, Department of Employment and Labour Relations, Occupational Health and Safety Branch would like to acknowledge the participation of the Hotel Newfoundland (A Canadian Pacific Hotel) who so freely gave their time and resources to assist us in the development of this case study.
- Fact sheet confirmed current: 2016-01-08
- Fact sheet last revised: 2021-12-17